What We Offer
Are you looking to scale your biotech process to an industrial scale? Do you require additional production capacity for an established process?
At Corden BioChem, we provide comprehensive support to our customers and their products from technology transfer to piloting, upscaling, process optimization, and ultimately the production of high-quality, certified commercial products.
Our Technologies
- Fermentation
Our 3,000 L pilot fermenters allow us to simulate the characteristics of our 120,000 L fermenters. This enables us to generate scalable process know-how for large-scale production.
read more
- Pilot bioreactors: 2 x 3,000 L stainless steel, stirred fermenters
- Production bioreactors: 19 x 120,000 L stainless steel, stirred fermenters
- Seed fermenters and buffer tanks of various sizes
- High agitation power input
- Process monitoring: DO, pH, temperature, pressure, mass flow, others
- Process modes: Batch, fed-batch, fill and draw, continuous harvest, others
- Anaerobic and aerobic processes possible
- Various carbon sources and customer-specific feeds possible
- Continous operations: 4 shifts, 365 days, 24/7
- Organisms: bacteria, yeast, filamentous fungi, microalgae, with both wild type strains and genetically modified organisms (GMOs) up to biosafety level 1
- Different filling options for culture broth: Tank containers, tank trucks, IBCs, others
- Direct connection with commercial-scale DSP facility for further processing
- Downstream Processing
We operate a state-of-the-art, highly automated, large-scale DSP facility. We have a range of bench- and pilot-scale equipment that allows us to simulate the characteristics of our large-scale DSP before upscaling.
read more
- Separators, e.g., disc stack centrifuge
- Crossflow & spiral wound membrane filtration systems (MF / UF / RO)
- Adsorption & ion exchange chromatography
- Enzyme reactors
- Crystallization and precipitation
- Blender
- Belt filter
- Continuous thin-film dryer
- Different filling options: Tank containers, tank trucks, IBCs, filling cabin for contained packaging
- Continous monitoring: 4 shifts, 24/7 all year around
- Food-grade facility (FSSC 22000)
- Option of setting up customized process equipment or process lines
- Cooperation network with external parterns, e.g., for spray drying
- Analytics & Quality
We have a comprehensive set of instruments for process monitoring & release testing as well as established measures to ensure delivery of high-quality product.
read more
- Raw material control, in-process monitoring and product realease testing via HPLC, GC, spectrophotometry, enzymatic tests, many others
- Separate fermentation lines for Food-grade (FSSC 22000) and technical products
- FSSC 22000 certified and FDA registered facility
- Religious certification for Halal and Kosher upon request
- On-site warehouse capacities for raw and auxiliary materials and end product storage at different temperature
- Waste management incl. biogas plant, on-site waste water treatment
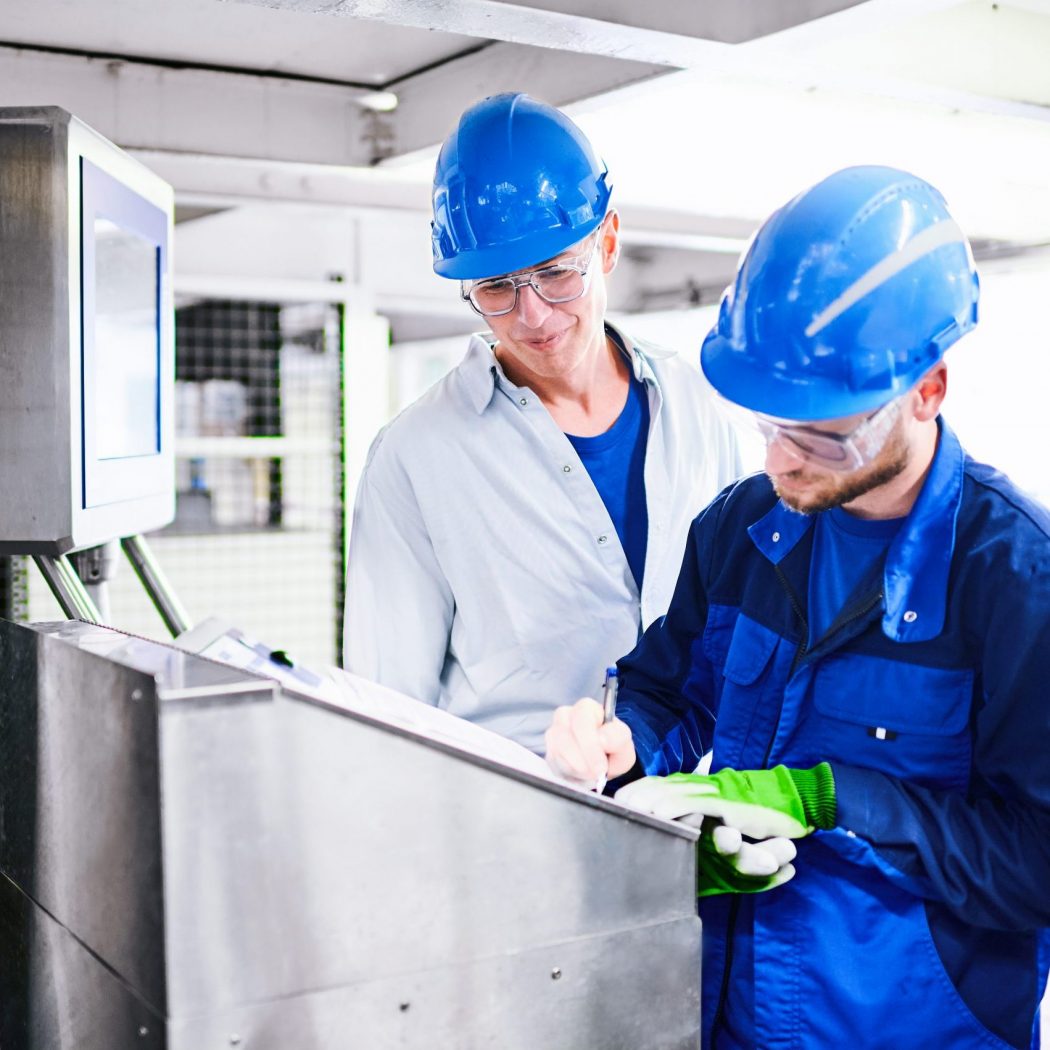
Upscaling services
Our expertise lies in effectively transferring processes from the pilot-stage to large-scale production.
We work closely with our customers to gain a comprehensive understanding of their production process, required technology, services, and desired product volumes.
We assess the compatibility of our facility with the customer’s requirements through a high-level gap analysis.
Based on the information gathered, we provide an initial non-binding offer outlining our services.
Once a cooperation framework is established, the technology transfer process begins.
We conduct a detailed evaluation of the customer’s process and adapt it, if necessary, to align with our equipment and capabilities.
The exchange of production strain, process information, analytical methods, and accompanying documentation takes place to facilitate a seamless transfer.
We conduct one or several test fermentations in a 3,000 L scale to validate the technical setup and generate tech-grade test material.
If required, downstream processing is tested in laboratory and/or pilot-scale settings.
We customize our facility to accommodate the specific needs of the customer’s process, implementing new equipment, if necessary.
The first large-scale fermentation takes place in one of our 120,000 L gross volume fermenters to demonstrate the technical feasibility of the production process.
We generate first higher volumes of product during this stage, including downstream processing of the fermentation broth to product concentrate or powder, if required.
In subsequent batches, we continuously evaluate and improve the process performance by varying process parameters and ensuring process reproducibility.
Contract Manufacturing
We manufacture your product on a large scale, ensuring adherence to strict quality control measures and conformity to product specifications.
We are open to customizing our equipment to suit your specific product requirements. Please reach out to discuss our options.
We use our extensive process knowledge and expertise in operating our equipment, and strive to improve process performance, titers, and yields from one production campaign to the next.
We offer a range of flexible business models, including campaigning, annual contracts, several-year contracts, pay-per-batch, pay-per-kilogram, as well as strategical partnerships.
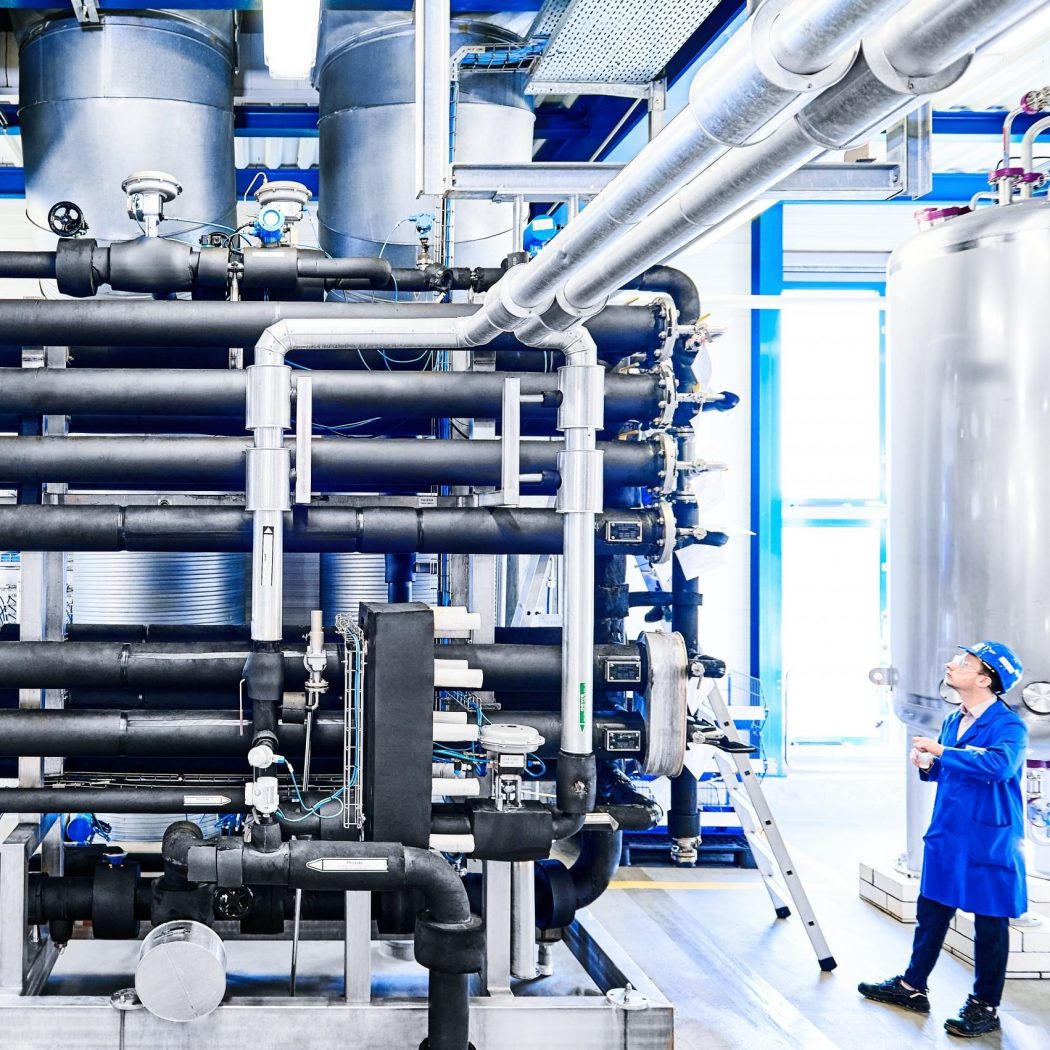